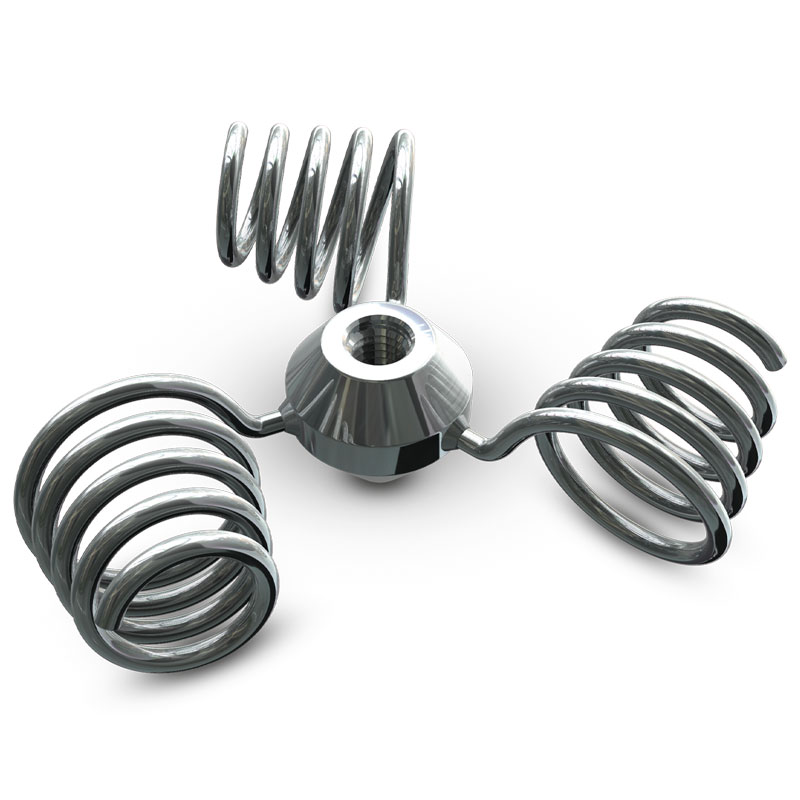

Groundbreakingly good
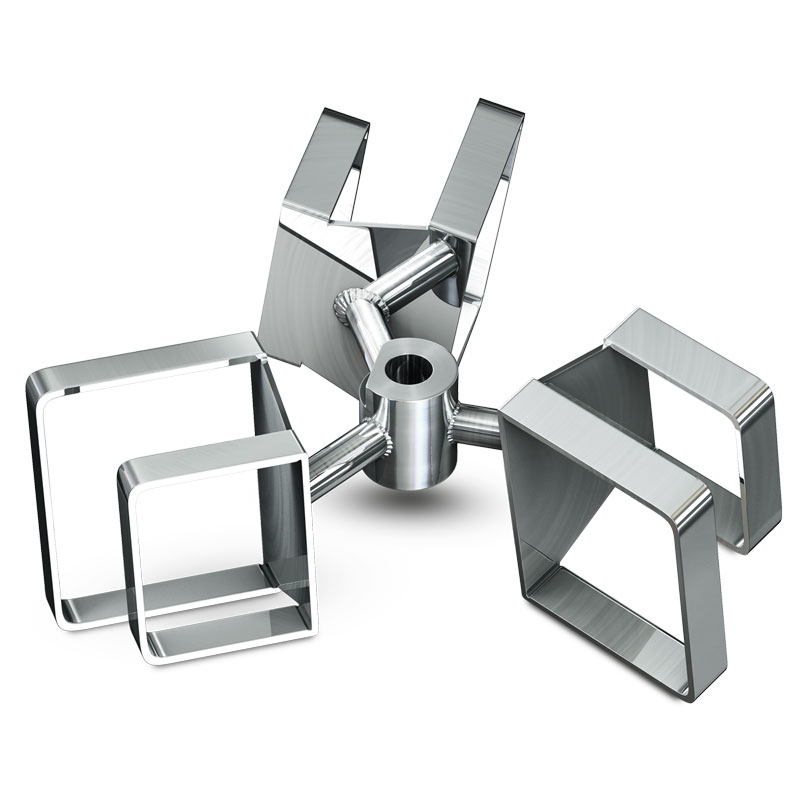
Saves energy, time and costs.
The VISCO JET® CRACK geometry makes it possible to break up agglomerates as well as simultaneous homogeneous distribution during the liquid phase, thus combining two agitation processes into one. This leads to a
significant increase in process efficiency in our customers’ production.
- Can be used for media with a viscosity up to 200,000 mPas
- The square design of the mixing element and the breaking edges at the cone inlet serve to efficiently break up the agglomerates (connected primary particles)
- Intrinsically dynamic mixing movements due to accelerated laminar flows at the cone outlet and turbulence at the cone inlet create the typical VISCO JET® flow pattern
- Comparatively low speeds for an energy-efficient agitation process
Highlights
Well thought-out, right down to the smallest detail
Especially in the paint and varnish sector, for the production of ceramic components and the manufacture of resins or putties, as well as in food production, dispersions are essential components of the manufacturing process. In this process, agglomerates are broken up by the application of shear forces and uniformly wetted with the liquid or pasty phase, usually an additive.
For a successful agitation process, two successive process steps are often used. The agglomerates are first broken up with a dispersing disc and then homogenised with the liquid phase by using an additional mixing element.
The VISCO JET® CRACK combines two mixing processes in one and is therefore the ideal solution for your agitation application from laboratory scale to production!
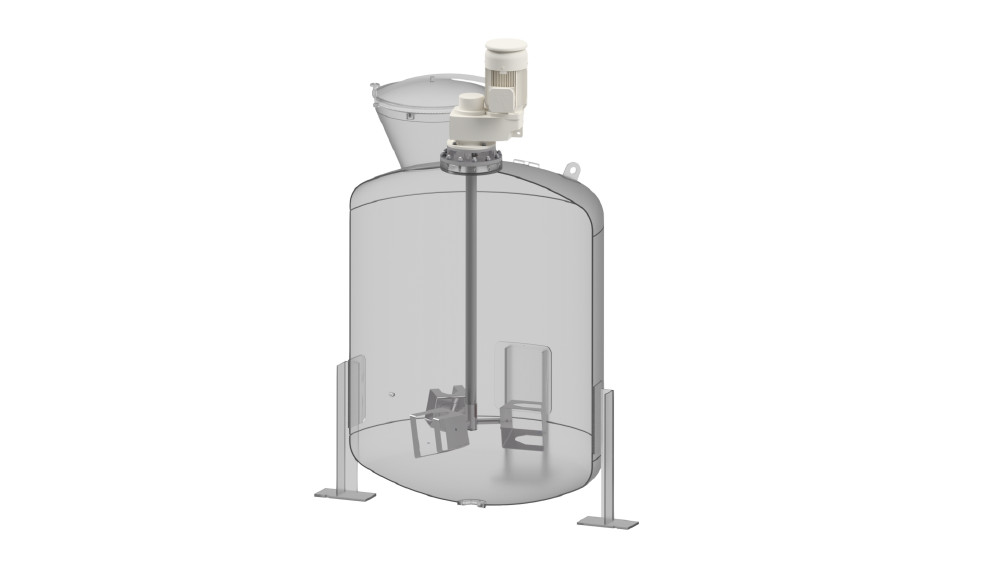
- 2-fold or 3-fold design of the impeller cones
- Standard version up to a impeller diameter of 2,000 mm
- Individual sizes also available on request
- Stainless steel 1.4301, 1.4404, 1.4571
- Ground version with Ra<0.8 μm or Ra<0.4 μm
- Installation in combination with several stirring levels and residue stirrer
- Individual material according to customer requirements, e.g. Superduplex or Hastelloy
- Additional coatings for an extremely long service life
- Tornado version for use in IBC containers
More information
Have you found what you’re looking for? We would be happy to show how you can benefit from using the VISCO JET® CRACK based on your process requirements!
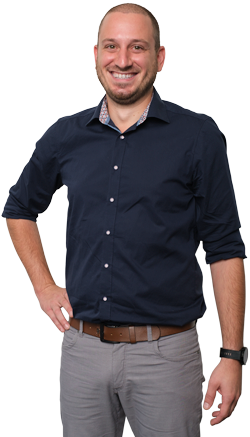
Similar products
You know about it and want to tackle it?!
… or we’ll call you back:
Nothing is as valuable to us as your time. That is why we are happy to prepare specifically for you. We will call you at your preferred time and clarify your questions. This is how we save your time and make your project successful with VISCO JET® solutions! We look forward to seeing you!